The fishmeal screening machine is an important fish meal re-processing equipment in the fish meal production line, which is mainly used to sieve out the fine fish powder according to the required size of the fish meal materials. It is also called the drum screen. Actually, this sieving machine can be widely used in many fields for screening all kinds of powdery materials, such as sawdust, sand, distiller grains, cement, lime, and so on.
Main components of the fishmeal screening machine
The fish meal screening machine is mainly composed of motor, reducer, drum device(rotation shaft and screen mesh), frame, sealing cover, inlet, and outlet. According to the actual production needs of customers it can be customized for the more reasonable design. Its foot can be both the fixed type and the removable type with wheels.
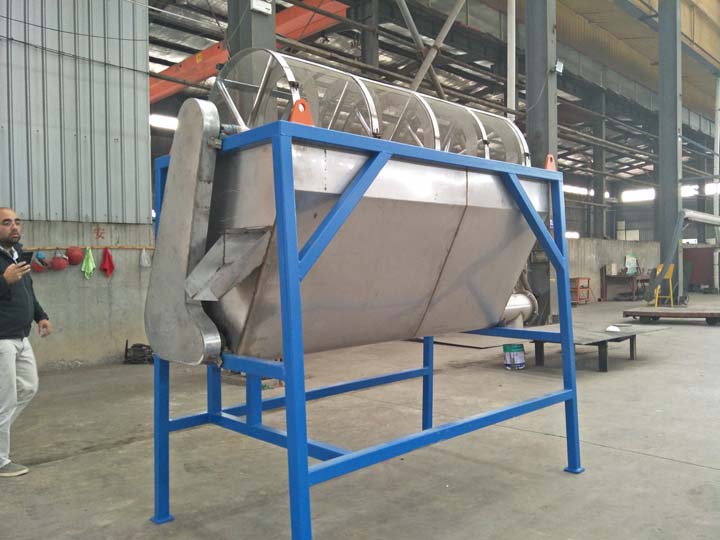
How does the fish meal sieving equipment work?
Typically, the drum unit of the machine is mounted obliquely to the frame for quick discharging of the powdery materials. When the drum screen is in operation, the motor is coupled to the drum unit through the coupling, and the drum unit is driven to rotate about its axis. The screening device of this fish meal screening machine has a plurality of screens of parallel sieve bars, and its screen can disassemble and replace screens of different mesh sizes.
After the fishmeal or other materials are placed in the feeding port of the machine, the material will quickly enter the sieving unit of the machine. Due to the tilting and rotation of the roller device, the material is turned over and rolled, and the materials can be screened out one by one by the screen mesh. The qualified fine particles are discharged through the screen outside the drum, and the unqualified large particles are discharged through the end of the drum. The material stuck in the mesh hole can also be ejected to prevent clogging.
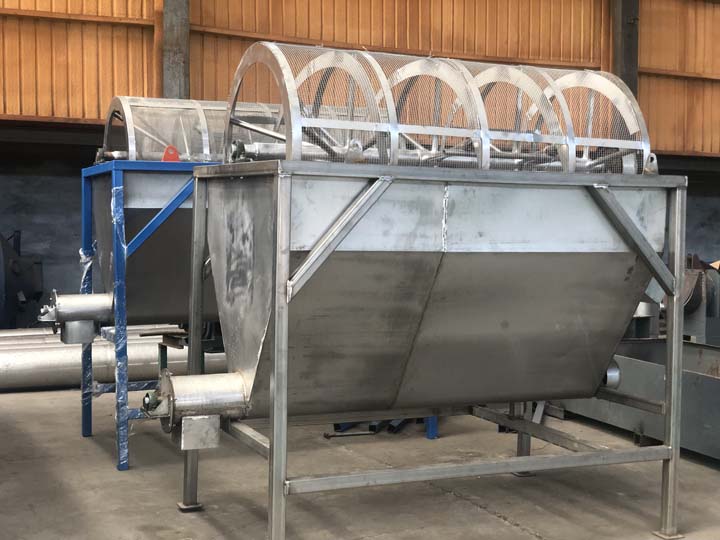
Applications of the fish powder screening machine
This screening machine is a new generation of screening equipment. Except for sieving the fishmeal powder, it can also be widely used in chemical, coking plants, mining, power plants, building materials, metallurgy, and other industries. Drum screen is often used for the classification of powdered materials, and its screening effect is very good.
Main features of the fish meal screening equipment
- The machine adopts the principle of rolling conveying, the friction coefficient is small, the wear is light, and the mesh holes are not easy to be blocked.
- The roller support adopts an integral through-shaft structure, which runs smoothly, does not vibrate, and has low noise.
- The internal drum screen accessories of the fish meal screening machine adopt the split design, which is simple in structure, quick and convenient to replace and repair.
- Screens of different materials and various mesh sizes can be customized according to customer requirements. High screening efficiency, long service life, and low maintenance cost.
- The drum body adopts an effective full-sealing structure, which does not cause dust or pollution. This fishmeal sieving screen device occupies a small space and is convenient for process layout.
Use precautions for fishmeal sieving machine
- The drum screen must be turned on before turning on the feeding device. The feeding device must be turned off before closing the device, and then the fish meal screening machine is turned off.
- It is strictly forbidden to make relevant adjustments when the equipment is running.
- Regularly check the drum screen and handle the corresponding problems in time. The machine should be inspected every day for the first three days after using this machine.
- Regularly check the lubrication of the bearing housing and gearbox of the machine. Under normal circumstances, the grease should be added once every 2 months, remember not to be too much, otherwise, it will easily cause the bearing to overheat, and clean the bearing once a year.
- Equipment that has been deactivated for a long time should be remotely tested for motor insulation before restarting to avoid burnout.